Laser Cutting is a very popular technique used across many different industries. But how does it actually work?
Lasers and why they are used for cutting
Laser stands for Light Amplification by Stimulated Emission of Radiation. These days, Lasers are used for many different purposes. The most popular area is cutting of materials like stainless steel, mild steel, aluminum, wood, plastics and many others. This process is very accurate and provides excellent quality cutting with a very small heat-affect zone. Laser is also used for engraving and etching of materials. This means that laser is an ultimate solution for decorating, packaging, manufacturing, construction, electrical and other applications.
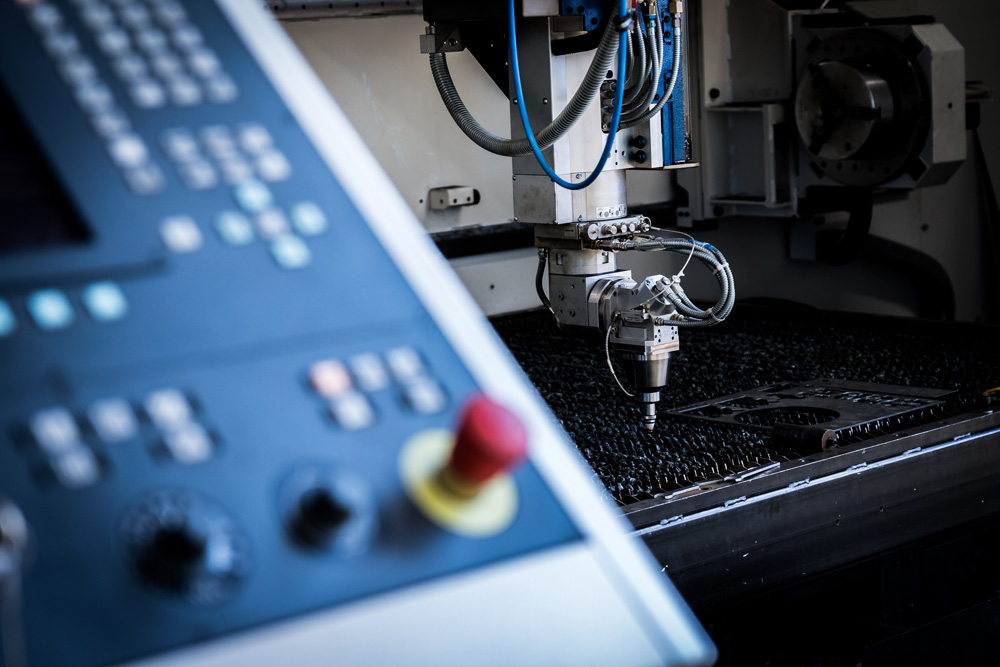
What is the laser cutting process?
A column of very high intensity light is called a laser beam. In most of CO2 lasers, the beam travels from the laser resonator, which creates the beam, through the machine’s beam path. Mirrors are typically used to direct the beam to a lens, which focuses the light at the work zone. The focused laser beam goes through the bore of a nozzle right before it hits the plate.
A special lens or a curved mirror does the focusing of the laser beam. This process takes place in the laser cutting head. The beam has to be focused very precisely so that the shape of the focus spot and the density of the energy in that spot are consistent, perfectly round and centred in the nozzle. A jet of air, oxygen or nitrogen is also passed through the nozzle. Because a large beam is focused to a single very small point, the heat density at that spot is extreme.
On CNC laser cutters (such as the Amada LCG3015 used by LaserSpeed), the laser cutting process is controlled by special software. Using the special drawings file, the laser cutting head is moving over the metal plate in the shape that is specified by this file. There are many parameters that are controlled by the CNS laser cutter to ensure high quality and a very accurate cutting process.
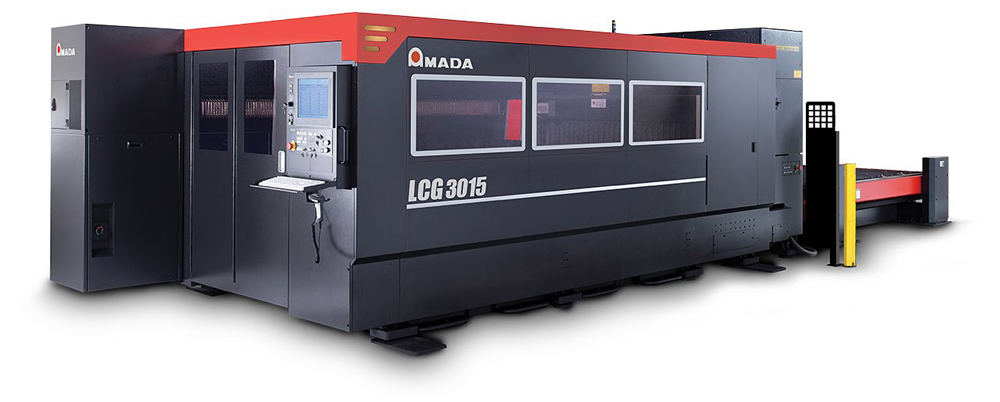
Advantages of laser cutting
Laser cutting has many advantages apart of high quality and accuracy. For example, mechanical cutting is more time consuming and not that effective in terms of saving materials. Laser cutting has no cutting edge which means that there is less material wasted after work is done. Because laser systems have a small heat-affected area, there is a lower risk of damaging the material. It is also possible to cut some materials that are difficult or impossible to cut by more traditional means.
Laser cutting has a couple of advantages over waterjet and plasma cutting. Laser is more accurate and more energy efficient. Modern laser machines operating at higher power are approaching plasma machines in their ability to cut through thick materials, but the capital cost of such machines is much higher than that of plasma cutting machines capable of cutting thick materials like steel plate.
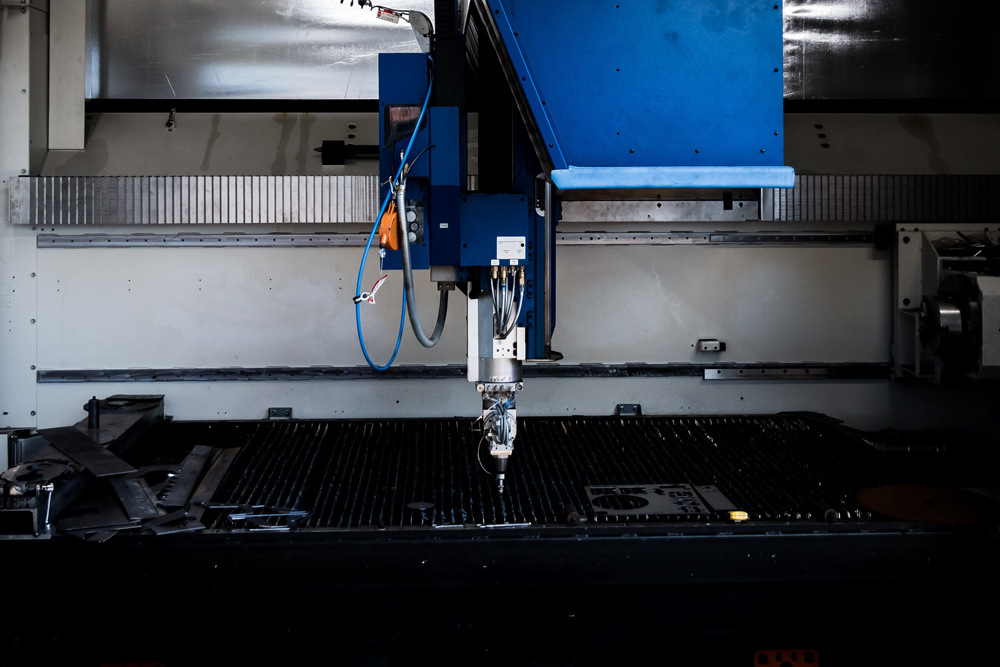
Laser Cutting with LaserSpeed
LaserSpeed aims to make the laser cutting process easy. Having a team of professionals on-site, customers just need to have an idea of product they want to have and LaserSpeed will do everything: drawing design, selection of correct materials, take care of the cutting process and deliver it right to your door. To learn more about laser cutting and other available services provided by LaserSpeed, please visit our website or talk to our friendly team.